Is neck turning a waste of time and effort?
Of all the topics that have been written about reloading, perhaps none is more controversial than turning the neck. It raises the hairs on the back of many people’s necks. It works?
The fact is that in some cases it is imperative to thin the neck to a certain thickness so that it can penetrate the rifle’s chamber. A benchrest rifle can be a case in point; a custom rifle for long range work may be another. In such cases, there is simply no argument.
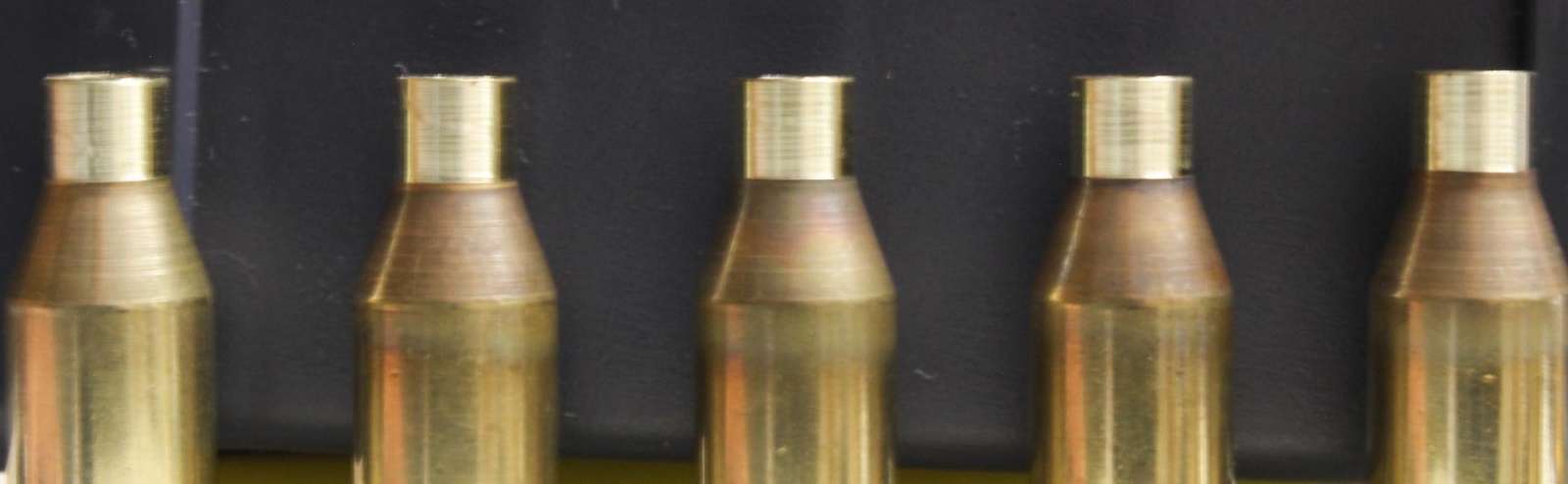
The discussion heats up when you suggest that turning the neck is beneficial on factory long-range or varmint rifles. Experienced long-range shooters have often said they can’t tell a difference in cartridge performance at any range.
Others claim that a turned neck in a factory rifle merely increases the gap between the edge of the neck and the chamber of the rifle.
It’s possible that any power increase is so small that it’s unmeasurable, but combined with other work on the cartridge case, makes a good group.
I have turned necks, primarily in .22-250 Remington and .243 Winchester cartridges for long range use with lighter projectiles to increase cartridge performance.
Did it work? I can’t say, but I do agree with our benchrest cousins who claim that thick necks are easier to maintain than thin ones.
I still doubt it’s a waste of time with factory guns and think the benefits are hard to measure.
I would suggest that the outcome is like reloading: you have to decide if the process is beneficial for your circumstances and cartridges.
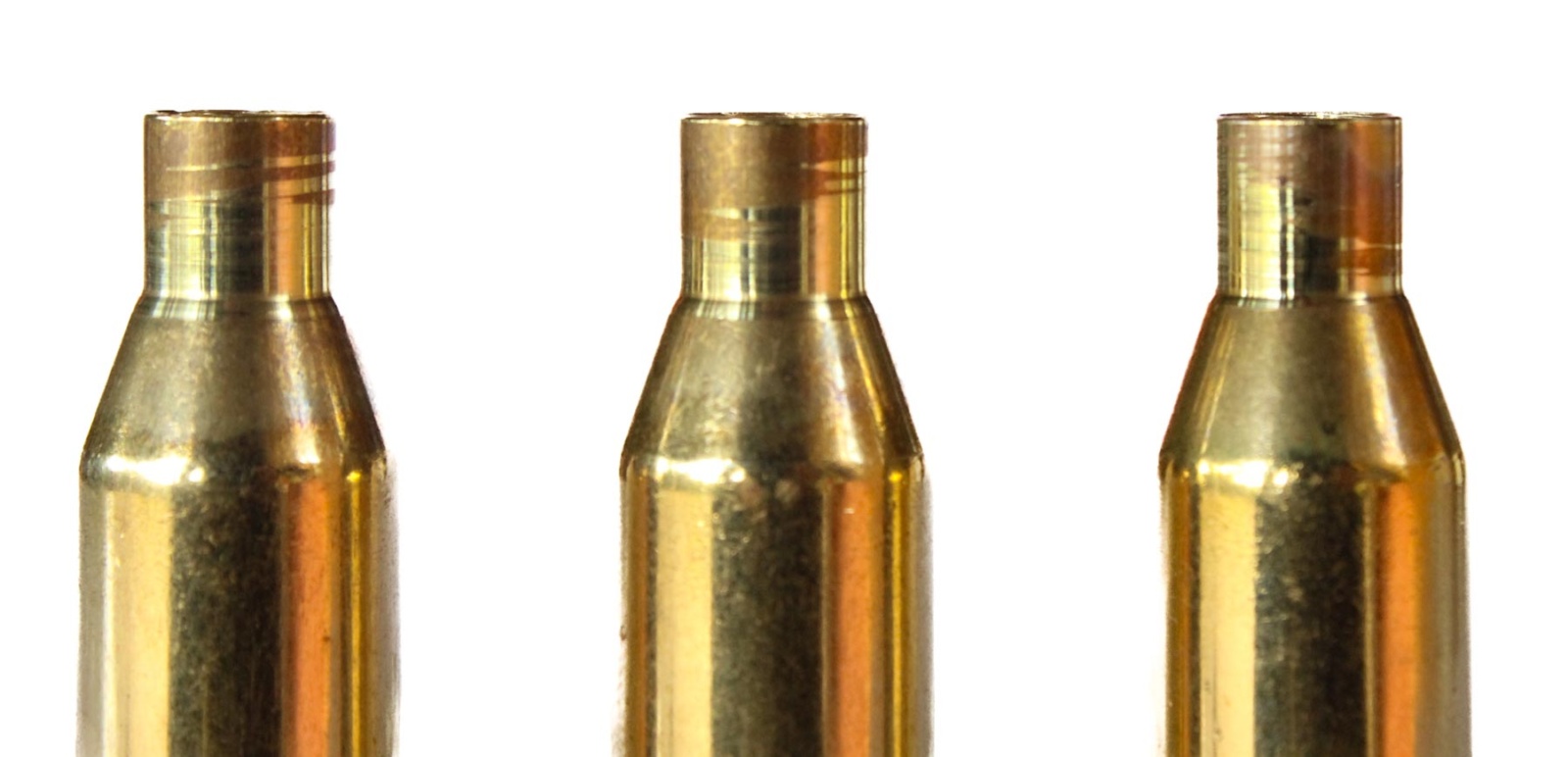
There are many good tools to carry out the process. Before you begin, make sure you have a few other must-have tools. The first is a set of feeler gauges that allow you to precisely set the cutter. Second, you need a ball micrometer to accurately measure neck thickness.
Before you start turning, you need to expand or contract the neck of the case so it sits snugly on the mandrel. If the fit is sloppy, the turned neck will not be right.
It’s much better to make several small cuts than to try one big one. The cut should just touch the end of the sloping shoulder.
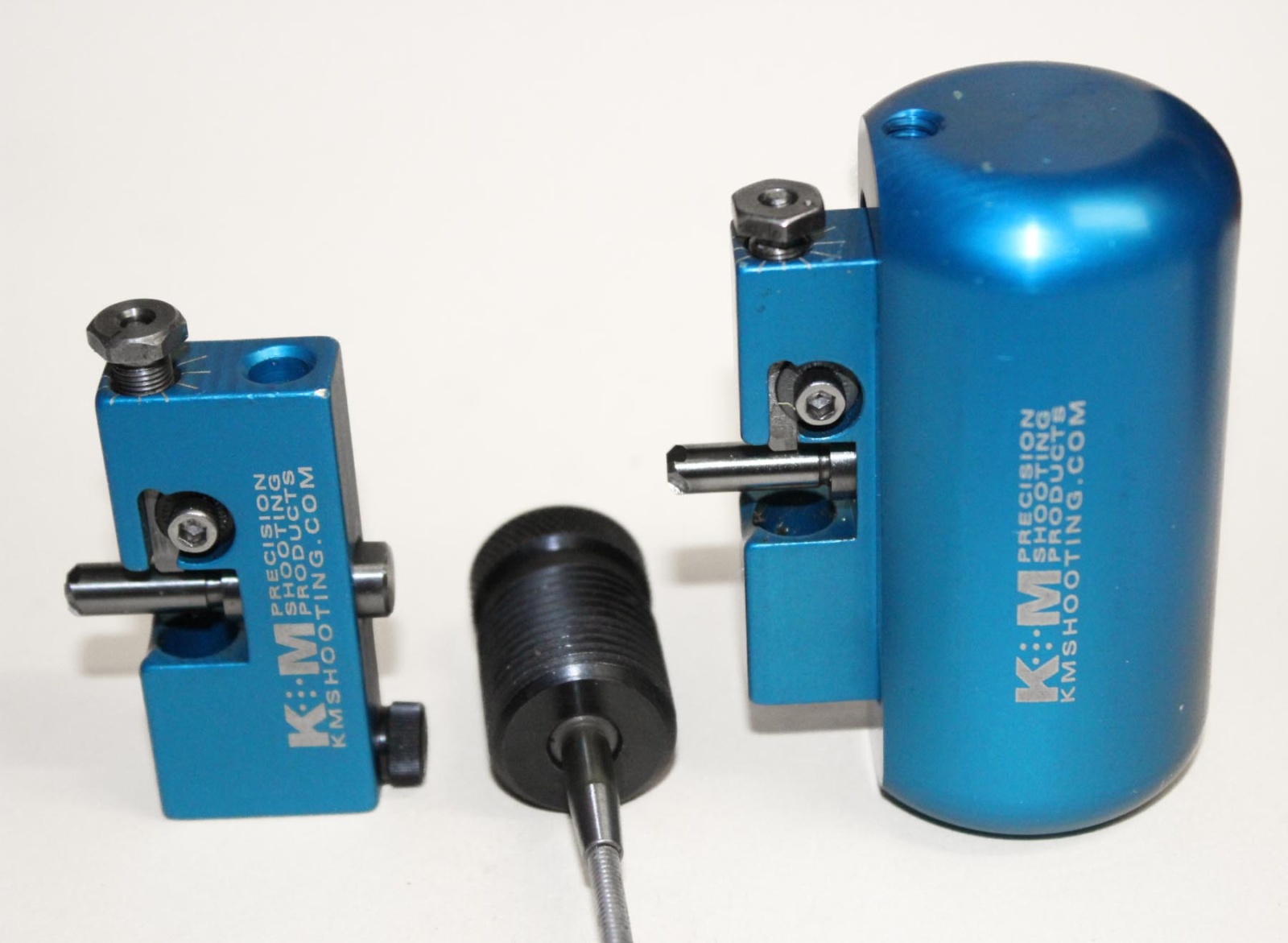
Lubrication is important. Don’t skimp on it.
Use a disposable case to set the cutter to the correct depth. This may require multiple attempts. Don’t rush and check the neck thickness often to make sure the cut stays correct.
For tabletop rifles, it is common for the expansion between the case and the chamber wall to not exceed 0.001 inch (0.025mm).
With a factory rifle, it’s up to you whether you cut off part of the case circumference or the entire circumference – it can be worth experimenting.
Be very careful with thin necks which are very easy to pinch. I suggest such necks should be annealed every time they hit the reload bench.