How to extend trailer life
With long lead times in factories, the increasing adoption of drop-and-hook freight, and more, trailers are suddenly finding a new lease of life in the trucking industry. a lot of higher – initial cost.
David Giesen, vice president of sales and marketing for Stoughton Trailers, told industry researcher FTR’s annual transportation conference that the cost of a dry truck has doubled in the last three years. Some customers have experienced up to eight price increases since the initial offer until final acceptance of the device.
“If they have the option to cancel their order, they don’t want to cancel,” he said of customers.
Higher purchase prices are not the result of opportunistic trailer manufacturers increasing their margins. They themselves struggle with the higher raw material costs that go into making a trailer, combined with supply chain-related component shortages and a lack of people to actually build the equipment.
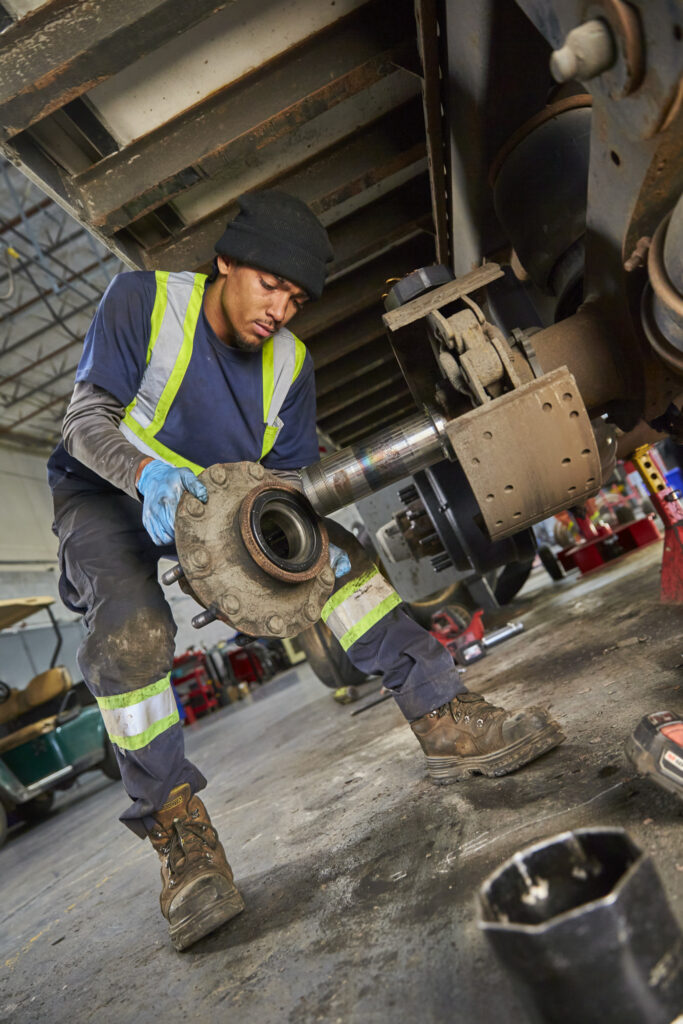
“At the end of the day, the trailer is made of raw materials,” Aaron Gorman, vice president of sales for Manac – Ontario and Western Canada, said in an interview with TruckNews.com. “Steel, aluminum, wood, rubber and plastic.”
Steel and aluminum prices have been particularly volatile in recent years as global economies emerge from pandemic-related manufacturing shutdowns. The good news is that Gorman is returning some stability in commodity prices, which may help stabilize trailer prices.
“Could you come down? Yes. At pre-pandemic prices? Absolutely not,” he said.
Giesen gave a similar response when asked about the prices by an attendee at an FTR conference. “My expectation is that the prices that are in place now will remain so into 2023,” he said, adding that lower raw material costs don’t necessarily translate into cheaper trailers. The conversion fees levied by aluminum mills, for example, mitigated the price relief on rails that the manufacturer had hoped for when aluminum prices fell.
Increasing inspections and maintenance
With supply shortages or trailer acquisition costs not ending immediately, maintaining this often-overlooked asset has suddenly become the focus of technicians and fleet maintenance managers. For others, trailers simply operate longer — but lengthening trade cycles without proper maintenance comes with its own risks.
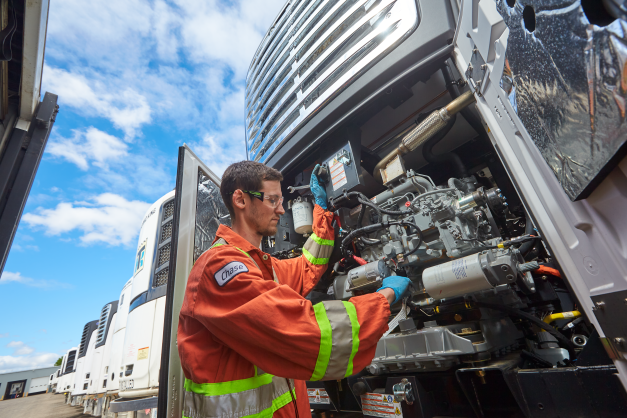
“Many units that would have been retired or put into storage are still on the road,” Gorman said.
His advice to fleets looking to extend trailer life is to step up equipment inspections. “In addition to the annual safety inspection and driver trips, we recommend additional preventative maintenance inspections throughout the year. Retighten the nuts on the wheel ends, [monitor] Adjust brakes, lubricate where and when needed,” he advised, and when adding LED lights, sufficient dielectric grease must also be applied to ensure longer life.
Pay special attention to the undercarriage, slack adjusters, fork pins and other moving parts, he added. Jamie Hillier, vice president of operations and maintenance at Trailcon Leasing, agreed and suggested keeping an eye on the TAB (tires, airlines and brakes) just like you would at a pub.
“If a driver or maintenance technician looks at these three points, they can easily add significantly to the life of the trailer,” he said. That means more than hitting tires with a hammer at a priority check to indicate roadworthiness.
“Make sure you glue hoops [with an air gauge],” he said. “Put in the gauge and see what the actual pressure is. Check the air lines for cracks and listen for small audible leaks. These could be bad for you if the trailer in the middle of nowhere has a Has broken down. Make sure the lines are not worn, frayed or puckered. Check the brakes to make sure there are no cracks and that they are adjusted. Every trailer that comes into our service bays, that’s the three Things we look at constantly and diligently.”
Extending the life of the device
With more than 10,000 trailers in its own network and the responsibility for the maintenance of another 20,000 customer trailers, Trailcon reacted quickly to the delivery bottleneck. When Hillier heard earlier this year that there was going to be a brake drum shortage, he bought two containers full of them and stocked the components at his Brampton, Ontario facility.
“In the past we’ve ordered a skid here or there,” he said.
Now the focus is on extending the life of the equipment as much as possible. “Make sure you treat this component like a wet rag,” he tells the techs. “You have to squeeze as much water as possible out of every part of this component. In times of part uncertainty, bringing that component to life is critical.”
Trailcon has added two new programs to help fleets safely extend trailer life. TrailerCare is a full-service leasing program that includes additional inspections by the company’s licensed technicians to extend life. A new Reefer Refresh program has been added for refrigerated fleets. This requires a comprehensive inspection of the trailer refrigeration unit (TRU) after approximately 30,000 hours of operation, when problems usually arise.
The company replaces or remanufactures wearing parts such as compressors, condensers and starters, and then adds another PM based on that chiller’s specific use case. Some fleets do their own renovations to get a few extra years of use out of their trailers.
do the renovation yourself
Lloyd De Merchant, manager of fleet maintenance at Moncton-based Keltic Transportation, said he will sandblast and paint the bogie of an aging trailer and inspect, repair or replace anything that is corroded. It has even replaced side panels on van trailers and has seen up to eight to ten additional years of use.

Gorman said DIY renovations are a good temporary fix in this environment, as long as they’re done right.
“We’ll see that for a while before we all catch up,” he said. “In doing so, the service centers and maintenance centers must also consider the overall structural integrity of the trailer. Points such as the deterioration of the floor over the years, the running gear and the overall condition of the structure of the trailer. If they pass a safety inspection, it makes sense to swap out other components around them.”
If anything good can come from this trailer supply shortage, it is that many of the practices introduced out of necessity to extend trailer life are likely to continue even as trailers become more readily available. It’s also forcing fleets and maintenance managers to place greater value on the low-profile trailer, traditionally viewed as little more than an inexpensive box on wheels.
“Some fleets have told me that the lack of equipment has made them more efficient.”
Aaron Gorman, Manac
“One thing some fleets have told me is that the lack of equipment has made them more efficient,” Gorman said. “They load and unload live more and make better use of what they have in their trailer pool.”
More drops and hooks
However, other fleets are increasing their trailer-to-truck ratios to better utilize drivers through increased use of drop-and-hook models. Few things might be harder to find than a new trailer, but it takes an experienced driver — and fleets tend to use drop-and-hook deliveries to keep drivers moving. However, this can create a new problem with trailers being left in the yard awaiting pickup instead of rolling down the freeway.
“There’s brake seizure and flat tires,” Gorman said of a few potential hazards. “They also get puddle water and snow on them. Fleets want to keep these trailers moving.”
As trailer prices rise, fleets are also paying more attention to specification for durability, something Gorman is pleased to see.
“Invest in the product from day one,” he advised. “Think about the application and where the equipment will be traveling…Heavy duty applications will require additional cross members and possibly extended slide rails, a few more roof bows in key high stress locations, a thicker, more robust tailgate frame assembly, a thicker floor and additional sealing throughout Follower. Nickel and diming over $100 [upgrades] has gone.”